Companies are constantly looking for ways to optimize their operations and provide better service to their customers. One area where technology has greatly transformed business processes is in the field service industry. Field Service Automation (FSA) has emerged as a game-changing solution that helps businesses streamline their operations and maximize their productivity. This article will describe the concept of Field Service Automation, explore its benefits, discuss key components, and provide insights on implementing and future trends in FSA.
Understanding field service automation
The concept of field service automation
Field Service Automation refers to the use of technology to automate and streamline various tasks performed by field service technicians. It involves integrating software, mobile devices, and other tools to improve efficiency, productivity, and customer satisfaction. By automating processes that were previously manual, companies can minimize paperwork, reduce errors, and provide faster and more accurate service.
Field Service Automation is not just about replacing manual tasks with technology; it also encompasses the transformation of the entire service delivery process. From the moment a customer request is received to the completion of the service, automation creates a seamless and efficient workflow. This results in improved response times, better resource allocation, and ultimately, increased customer loyalty.
The role of automation in field services
Automation plays a pivotal role in field services by simplifying and standardizing various processes. It enables technicians to access real-time information, collaborate with team members, and provide superior service to customers. By automating tasks such as work order management, scheduling, and inventory control, companies can optimize their resources, reduce costs, and enhance operational efficiency.
Furthermore, automation in field services allows for better data collection and analysis, leading to more informed decision-making. By tracking key performance indicators and service metrics in real time, companies can identify trends, anticipate customer needs, and proactively address potential issues. This data-driven approach not only improves service quality but also enables companies to stay ahead of the competition in a rapidly evolving market.
Benefits of field service automation
Enhancing operational efficiency
One of the primary benefits of Field Service Automation is improved operational efficiency. By automating workflows and eliminating manual processes, companies can minimize paperwork, reduce administrative tasks, and ensure timely completion of work orders. Automation also facilitates seamless communication between field technicians and other team members, enabling faster decision-making and problem-solving.
Moreover, Field Service Automation allows for real-time tracking of field technicians, enabling companies to monitor their progress and performance efficiently. This visibility into field operations helps in identifying any bottlenecks or inefficiencies in the workflow, allowing for prompt intervention and resolution. By having a clear overview of all ongoing tasks and their statuses, companies can optimize resource allocation and complete all work orders in a timely manner.
Reducing operational costs
Field Service Automation helps businesses reduce operational costs in multiple ways. By eliminating paperwork, companies can significantly decrease printing and storage costs. Automation also enables better resource allocation, efficiently scheduling and dispatching technicians to customer sites. This reduces travel time and fuel costs, resulting in substantial savings for the company.
In addition to the cost savings from reduced paperwork and optimized scheduling, Field Service Automation also contributes to minimizing overtime expenses. By streamlining processes and improving the efficiency of field operations, companies can ensure that tasks are completed within regular working hours, reducing the need for overtime pay. This not only cuts down on labor costs but also helps in maintaining a healthy work-life balance for field technicians.
Improving customer satisfaction
Field Service Automation has a direct impact on customer satisfaction. By automating the scheduling and dispatching processes, companies can respond to customer requests faster and provide accurate and reliable service. Automation also enables technicians to have access to critical customer information, such as service history, preferences, and equipment details. This helps technicians deliver personalized service and resolve issues more effectively, thereby enhancing customer satisfaction.
Furthermore, Field Service Automation empowers companies to implement proactive maintenance strategies, servicing equipment before any issues arise. This predictive maintenance approach not only reduces downtime for customers but also builds trust and loyalty by demonstrating a commitment to reliable service. By leveraging automation tools for preventive maintenance, companies can enhance the overall customer experience and differentiate themselves in a competitive market.
Key components of field service automation
Work order management
Work order management is a crucial component of Field Service Automation. It involves creating, assigning, and tracking work orders throughout their lifecycle. Automation streamlines this process, enabling companies to efficiently manage work orders, track their progress, and provide updates to both technicians and customers. This ensures that work orders are completed on time and customer expectations are met.
Effective work order management also helps companies analyze historical data to identify trends, optimize workflows, and improve overall service delivery. By leveraging automation tools, companies can generate insightful reports on work order completion rates, technician performance, and customer satisfaction levels. This data-driven approach empowers companies to make informed decisions and continuously enhance their field service operations.
Dispatch and scheduling
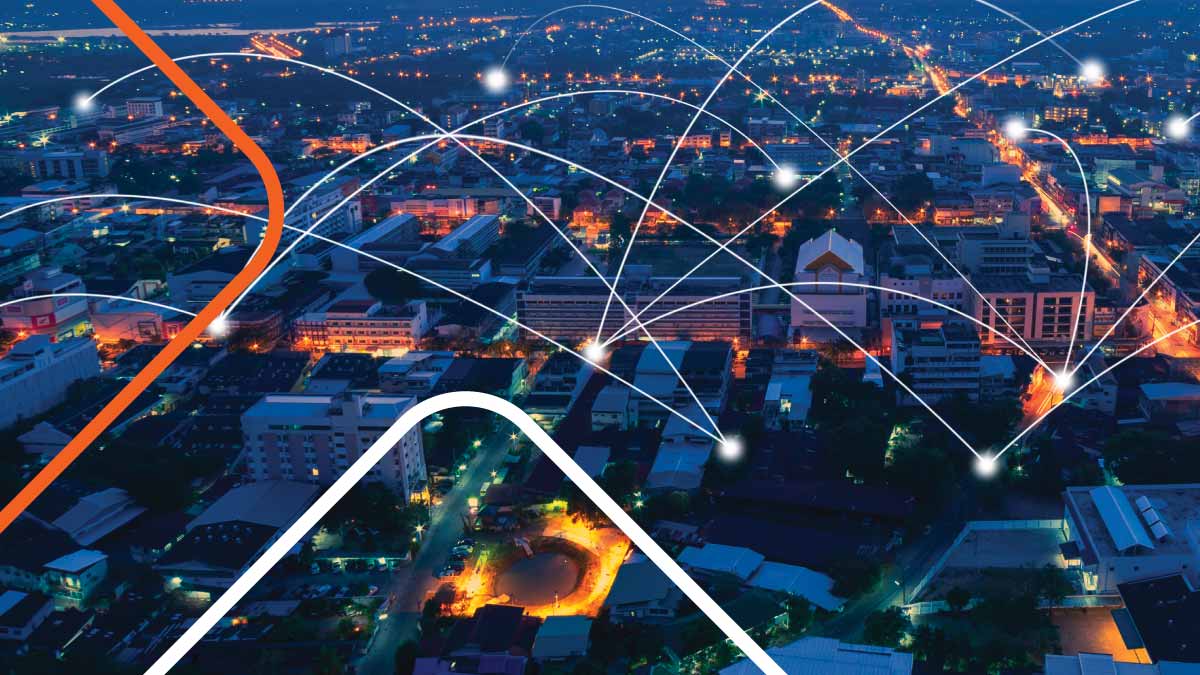

Efficient dispatch and scheduling are vital for field service operations. Automation enables companies to optimize resource allocation by considering factors such as technician skills, availability, and proximity to customer sites. This ensures that customers receive service in a timely manner and minimizes travel time and costs for technicians.
Furthermore, automation in dispatch and scheduling allows companies to proactively respond to service requests, prioritize urgent tasks, and dynamically adjust schedules based on real-time updates. By integrating predictive analytics and machine learning algorithms, companies can forecast service demands, anticipate potential disruptions, and proactively allocate resources to meet customer needs effectively.
Inventory management
Inventory management is another critical component of Field Service Automation. By automating inventory tracking, companies can ensure that technicians have the right parts and equipment to complete their tasks. Automation enables real-time visibility into inventory levels, reduces stockouts, and improves overall operational efficiency.
In addition to optimizing inventory levels, automation in inventory management enhances collaboration between field technicians and warehouse teams. By implementing barcode scanning, RFID technology, and IoT devices, companies can accurately track inventory movements, monitor consumption patterns, and streamline replenishment processes. This level of automation enhances inventory accuracy, reduces carrying costs, and enhances service delivery by ensuring that technicians have access to the necessary resources at all times.
Implementing field service automation
Steps to automate field services
Implementing Field Service Automation requires careful planning and execution. The following steps can help businesses successfully automate their field service operations:
- Assess current processes: Identify pain points, bottlenecks, and areas that could benefit from automation.
- Select the right solution: Choose a Field Service Automation solution that aligns with your business needs and offers the desired functionalities.
- Configure and customize: Tailor the solution to fit your specific requirements, such as workflow, reporting, and integration with existing systems.
- Train and educate: Provide comprehensive training to technicians and staff to ensure they understand the benefits and proper use of the automation tools.
- Monitor and evaluate: Continuously monitor the performance of the automation system and gather feedback from technicians and customers to identify areas for improvement.
Overcoming challenges in implementation
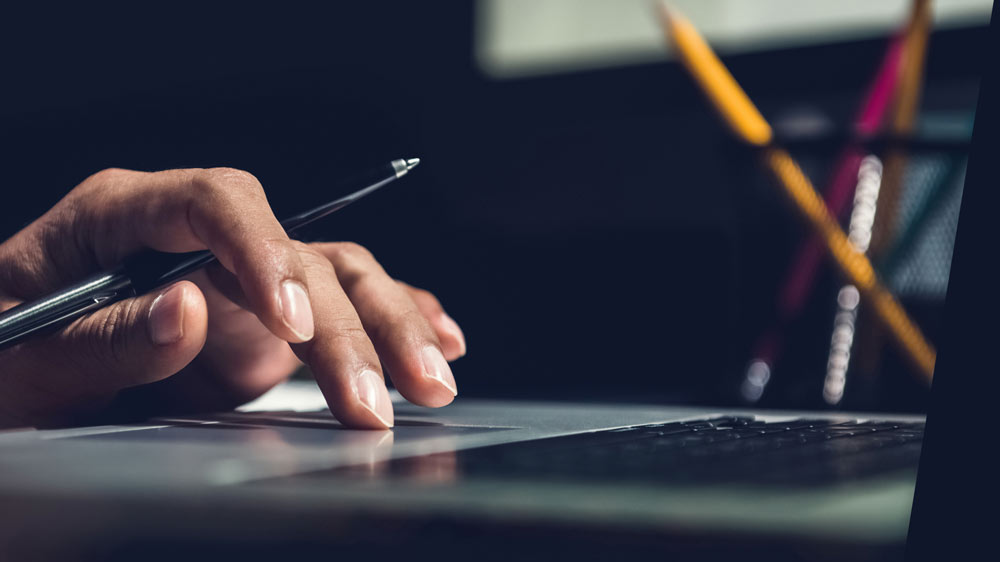
Implementing Field Service Automation may present challenges that need to be addressed. Some common challenges include resistance to change, lack of technical expertise, and integration issues with legacy systems. By proactively addressing these challenges and fostering a culture of continuous improvement, businesses can successfully deploy and leverage the benefits of Field Service Automation.
One of the key challenges in implementing Field Service Automation is resistance to change. It is natural for employees to feel apprehensive about adopting new technologies and processes. To overcome this, businesses can emphasize the benefits of automation, such as increased efficiency, improved customer satisfaction, and reduced manual errors. Additionally, involving employees in the decision-making process and providing them with proper training and support can help alleviate their concerns and encourage acceptance of the new system.
Another challenge that businesses may face is the lack of technical expertise. Implementing and managing a Field Service Automation solution requires a certain level of technical knowledge and skills. Luckily, businesses can consider partnering with a technology provider or hiring experts who specialize in implementing and supporting such systems. These experts can provide guidance, training, and ongoing technical support to ensure a smooth transition and successful implementation of the automation solution.
Future trends in field service automation
Predictive maintenance and AI
With advancements in Artificial Intelligence (AI) and Machine Learning, Field Service Automation is expected to move towards predictive maintenance. By leveraging AI algorithms, companies can predict equipment failures and schedule preventive maintenance before breakdowns occur. This approach helps businesses reduce downtime, extend equipment lifespan, and optimize their maintenance resources.
Predictive maintenance powered by AI is revolutionizing the way companies manage their assets. By analyzing historical data and patterns, AI can forecast when equipment is likely to fail, allowing for timely interventions that prevent costly breakdowns. This proactive approach not only saves money but also enhances operational efficiency and reliability.
Mobile field service automation
Mobile devices have become an integral part of field service operations. Mobile Field Service Automation solutions enable technicians to access information, update work orders, and communicate with customers and the office while on the go. The use of mobile devices empowers technicians to provide faster and more efficient service, resulting in improved customer satisfaction.
Furthermore, mobile field service apps are evolving to incorporate features like augmented reality (AR) for remote assistance. Technicians can now use AR to overlay digital instructions or diagrams onto real-world equipment, facilitating troubleshooting and repairs. This blend of mobile technology and AR is enhancing the capabilities of field service teams and streamlining maintenance processes.
IoT in field service automation
The Internet of Things (IoT) holds great potential for Field Service Automation. By integrating IoT devices with automation systems, companies can remotely monitor equipment performance, receive real-time alerts, and proactively address issues. This enables predictive maintenance, reduces downtime, and supports smooth operations.
Moreover, IoT sensors are not only transforming reactive maintenance into proactive strategies but also enabling the concept of “servitization.” With IoT-enabled equipment, companies can shift from selling products to offering services based on equipment usage data. This shift opens up new revenue streams and strengthens customer relationships through value-added services.
Conclusion
Field Service Automation has proven to be a game-changer in streamlining operations for businesses. By leveraging automation technologies, companies can enhance operational efficiency, reduce costs, and improve customer satisfaction. Key components such as work order management, dispatch and scheduling, and inventory management contribute to the success of Field Service Automation. Implementing FSA requires careful planning and overcoming challenges such as resistance to change and integration issues. Looking ahead, predictive maintenance, mobile solutions, and the integration of IoT are likely to shape the future of Field Service Automation. Embracing these trends will enable businesses to stay ahead of the curve and further streamline their operations.