Understanding the concept of wrench time
Technicians play a crucial role in ensuring the smooth operation of any industrial or manufacturing facility. One key factor that can significantly impact a field service technician’s productivity and potential is their wrench time.
Efficiently managing wrench time is not just about tracking hours spent on tasks; it is about optimizing the quality and effectiveness of those hours. By maximizing wrench or tool time, technicians can streamline their workflow, reduce downtime, and enhance the overall efficiency of maintenance operations. This emphasis on time management can lead to cost savings, improved equipment reliability, and a safer work environment.
Defining wrench (tool) time in the technician field
Wrench time (also known as tool time) refers to the actual time a technician spends working on equipment and performing value-added tasks. It is when technicians are actively engaged in hands-on activities such as repairs, inspections, or preventive maintenance. Wrench or tool time measures the technician’s efficiency and ability to deliver results.
Optimizing tool time involves more than just increasing the number of hours worked; it requires a strategic approach to task prioritization, resource allocation, and skill development. By implementing best practices in time management, organizations can empower their technicians to work smarter, not harder, ultimately driving operational excellence and sustainable business growth.
The importance of wrench time for technicians
Wrench time is a critical performance indicator directly impacting a technician’s overall productivity and success. By maximizing their tool time, technicians can accomplish more in less time, leading to increased job satisfaction and improved customer satisfaction. It allows technicians to fully utilize their skills and knowledge, unlocking their true potential.
Effective time management can foster a culture of continuous improvement within the technician field. By regularly evaluating and optimizing tool time practices, technicians can identify areas for enhancement, implement innovative solutions, and drive operational excellence. This proactive approach to tool time optimization benefits individual technicians and contributes to the organization’s long-term success and competitiveness as a whole.
The impact of increased wrench time
Increasing wrench time can have far-reaching benefits for both technicians and the organizations they serve. Let’s explore some of the key impacts of maximizing tool time.
Boosting technician productivity
When technicians spend more time on valuable activities, such as troubleshooting and repairs, their productivity levels soar. By minimizing non-value-added tasks and streamlining work processes, organizations can significantly increase technicians’ time on critical tasks, resulting in faster turnaround times and reduced equipment downtime.
Technicians can also dedicate more hours to preventive maintenance tasks. This proactive approach helps identify potential issues before they escalate into costly breakdowns, ultimately improving equipment reliability and longevity.
Enhancing skill development and mastery
Increased wrench time also provides technicians with more opportunities to master their craft. By allowing them to focus on hands-on tasks, technicians can refine their skills, gain valuable experience, and become experts in their respective fields. This not only enhances the technician’s individual career growth but also strengthens the organization’s overall technical capabilities.
Extended tool time allows technicians to engage in continuous learning and skill enhancement programs. This ongoing development ensures that technicians stay abreast of the latest technologies and industry best practices, positioning them as valuable assets to the organization and enabling them to tackle complex challenges confidently.
Strategies for increasing wrench time
Now that we understand the importance and impact of tool time, let’s explore some practical strategies to help organizations and technicians increase their tool time.
Wrench time is a critical metric in maintenance operations, directly impacting productivity, cost-effectiveness, and overall equipment reliability. Organizations can significantly improve operational efficiency and asset performance by maximizing the time technicians spend on actual maintenance tasks.
Efficient job planning and scheduling
Effective job planning and scheduling are crucial in maximizing wrench time. By properly planning and prioritizing tasks, technicians can minimize downtime and the need for unnecessary equipment setups or travel time. Additionally, organizations can leverage technology, such as computerized maintenance management systems (CMMS), to optimize job assignments, allocate resources efficiently, and minimize idle time.
Proactive maintenance planning, including predictive maintenance strategies based on equipment condition monitoring and historical data analysis, can help organizations anticipate maintenance needs and schedule tasks during planned downtime, optimizing wrench time utilization.
Reducing non-productive activities
Organizations need to identify and eliminate non-productive activities that consume valuable technician time to increase wrench time. For example, implementing standardized work procedures, optimizing inventory management systems, and providing technicians with easy access to tools and equipment can reduce time wasted searching for resources. Regular training and skills development programs can also help technicians improve their efficiency and minimize mistakes.
Fostering a culture of continuous improvement and empowering technicians to participate in process optimization initiatives can lead to innovative solutions for streamlining workflows, eliminating bottlenecks, and enhancing overall wrench time performance.
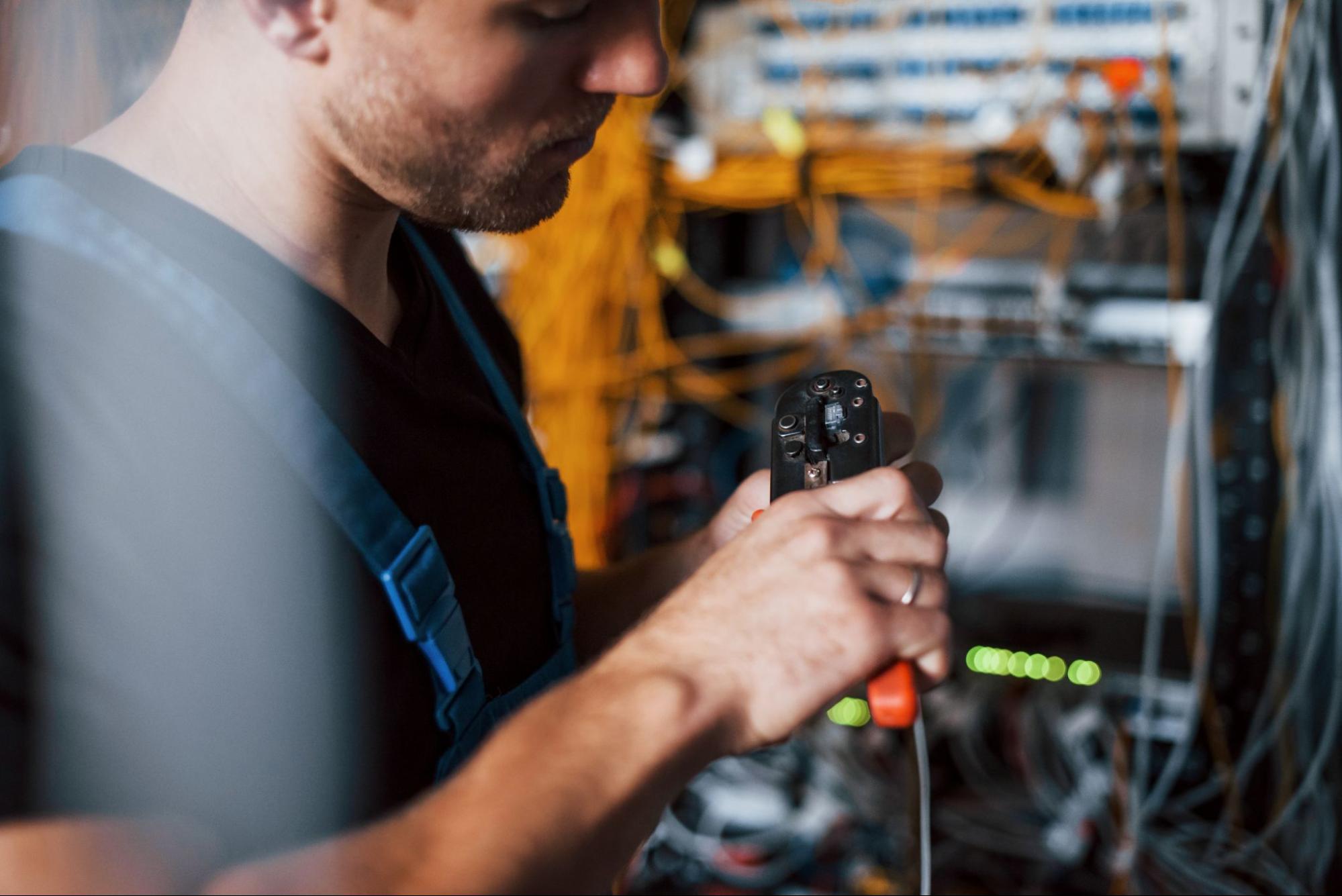
Overcoming challenges in increasing wrench time
While increasing tool time can lead to significant benefits, it is not without its challenges. Let’s look at some of the common hurdles organizations may face when trying to maximize wrench time:
Addressing technician resistance
Change can be met with resistance, especially from technicians who are accustomed to their existing work processes. To overcome this challenge, organizations should involve technicians in the planning and implementation of wrench time enhancement initiatives. By effectively communicating the benefits and addressing concerns, organizations can gain technicians’ buy-in and create a culture of continuous improvement.
Providing training and support to technicians during the transition period can help alleviate resistance. Offering resources such as workshops, one-on-one coaching, and access to online learning platforms can empower technicians to embrace new ways of working and increase their efficiency.
Managing workload and technician burnout
While increasing wrench time is essential, organizations must use a balanced approach to prevent technician burnout. Excessive workload and prolonged periods of high-intensity work can negatively impact technician morale and productivity. Organizations should adopt workload management strategies, such as effective shift planning, realistic task assignments, and periodic downtime for rest and rejuvenation.
Fostering a supportive work environment where technicians feel valued and recognized for their contributions can help mitigate burnout. Recognizing achievements, providing opportunities for skill development, and promoting work-life balance are essential components of creating a sustainable and healthy work culture.
Measuring the success of increased wrench time
Once organizations have implemented strategies to increase wrench time, measuring and evaluating their effectiveness is crucial. Key performance indicators (KPIs) can provide valuable insights into the success of these initiatives.
One key performance indicator organizations can track to measure the impact of increased tool time is the overall tool time percentage. This metric reflects the proportion of time that technicians spend actively working on value-added tasks. By monitoring this KPI, organizations can assess the effectiveness of their efforts in reducing non-value-added activities and maximizing productive time.
Another important KPI to consider is the average time spent on non-value-added activities. This metric reflects the amount of time technicians spend on tasks that do not directly contribute to completing a job. Organizations can further optimize time and improve overall efficiency by identifying and addressing these non-value-added activities.
In addition to these KPIs, organizations should also track equipment downtime as a measure of wrench time success. Organizations can minimize equipment downtime by ensuring technicians have uninterrupted access to the tools and resources needed to perform their tasks efficiently. This not only increases tool time but also reduces the frustration and delays caused by equipment failures.
Interpreting wrench time data for continuous improvement
Interpreting wrench time data is crucial for driving continuous improvement. By analyzing data trends and identifying patterns, organizations can make informed decisions about refining work processes, addressing inefficiencies, and investing in further technician training and development.
Regular performance reviews and feedback sessions also provide valuable opportunities for technicians to share insights and contribute to the ongoing optimization of tool time. By actively involving technicians in analyzing and interpreting wrench time data, organizations can tap into their expertise and experience to identify areas for improvement and implement targeted solutions.
Organizations can leverage the power of technology to enhance their analysis of wrench time data. Advanced data analytics tools can identify correlations between variables such as technician skills, job complexity, and tool time performance. By uncovering these relationships, organizations can gain deeper insights into the factors that influence tool time and make data-driven decisions to drive continuous improvement.
By continuously monitoring, evaluating, and improving wrench time performance, organizations can ensure that increased tool time remains a key driver of technician productivity and success. This ongoing commitment to optimizing tool time benefits the organization and empowers technicians to reach their full potential and deliver exceptional results.
Maximizing tool time is essential for enhancing technician productivity and operational efficiency. By leveraging solutions like the Field Nation marketplace, organizations can effectively leverage on-demand talent in their workforce and optimize wrench time, directly improving their maintenance operations and business outcomes.