A well-defined work order process is essential for efficient and effective operations in the field service industry. A work order represents a task or service request that needs to be fulfilled, and managing and executing these orders involves several key components and steps. This guide will explore the basics of the work order process, its importance, the key components involved, the steps to follow, and how to implement an effective work order process in your organization.
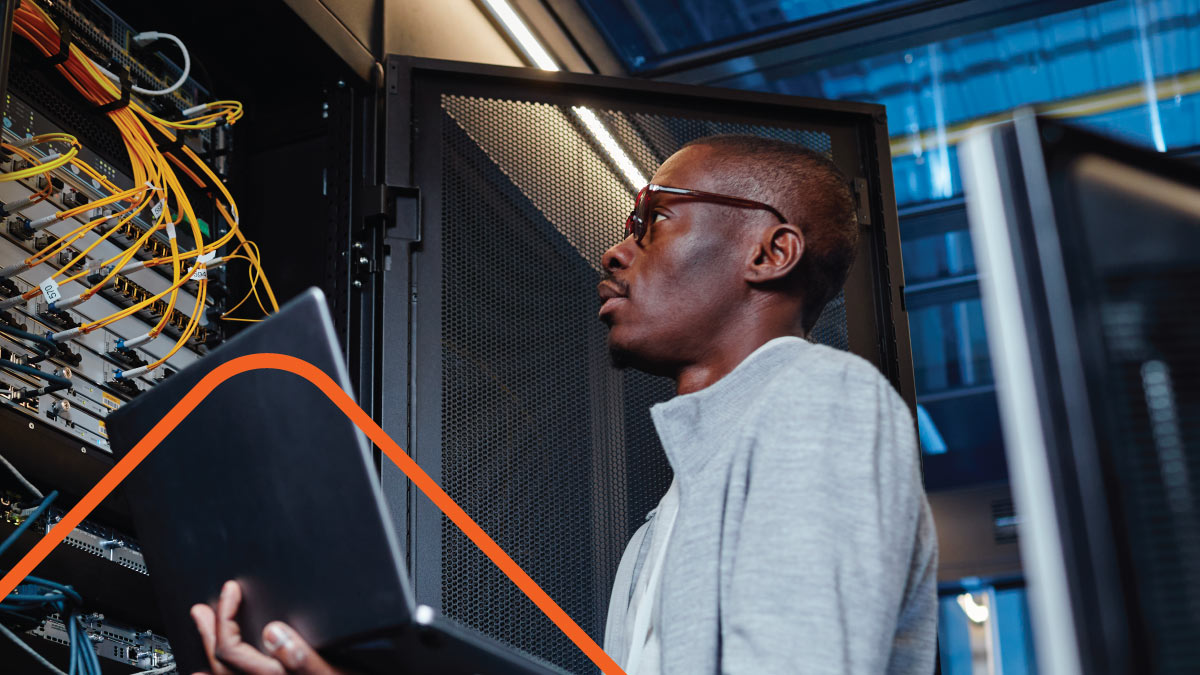
Understanding the basics of the work order process
The work order process is the systematic approach field service organizations use to manage service requests, assign tasks to the appropriate personnel, schedule and dispatch the work, execute the tasks, and document the results. It serves as a roadmap for delivering services promptly and efficiently.
Field service organizations often use specialized software to automate and streamline the work order process. This software allows for creating digital work orders, the real-time tracking of job progress, and integration with other systems such as inventory management and customer relationship management (CRM) tools. By leveraging technology, organizations can enhance the efficiency and accuracy of their service delivery.
Importance of the work order process in field service
The work order process plays a crucial role in field service operations by providing structure and clarity to service delivery. It streamlines communication and coordination between various stakeholders, such as customers, technicians, dispatchers, and managers. By following a standardized process, organizations can ensure that tasks are completed on time, resources are optimally utilized, and customer satisfaction is maximized.
Furthermore, the work order process enables organizations to track key performance indicators (KPIs) related to service delivery, such as response times, resolution rates, and customer feedback. By analyzing these metrics, organizations can identify areas for improvement, implement best practices, and ultimately enhance the overall quality of their services. This data-driven approach allows field service organizations to continuously optimize their processes and stay competitive.
Key components of a work order process
Below, we will discuss the details of the key components of a work order process, including job details and specifications, scheduling and dispatching, task execution, and reporting and documentation.
Job details and specifications
The first component of the work order process is capturing and documenting all the necessary job details and specifications. This includes gathering information about the service requested, such as location, problem description, equipment involved, and any specific instructions. It is essential to communicate the expectations and requirements to the technicians and other personnel involved in executing the work order.
For example, if a work order involves repairing a malfunctioning HVAC system in a commercial building, the job details and specifications would include the exact location of the system, the specific issue reported by the customer, the make and model of the equipment, and any safety precautions that need to be taken. This level of detail ensures that the technicians clearly understand the task at hand and can effectively address the problem.
Scheduling and dispatching
Once the job details are gathered, the next step is to schedule and dispatch the work to the appropriate personnel. This involves assigning tasks based on technician availability, skillset, proximity to the job site, and priority level. Efficient scheduling and dispatching ensure the right resources are allocated to the right jobs, minimizing delays and maximizing productivity.
For instance, in a large-scale construction project, scheduling and dispatching would involve coordinating multiple teams of workers, each assigned to different site areas. The scheduling process would consider factors such as the availability of materials, the progress of other tasks, and the need for specialized equipment. By carefully planning and coordinating the work, the project can stay on track and meet its deadlines.
Execution of tasks
After the work order has been scheduled and dispatched, the assigned technicians carry out the required tasks. This involves traveling to the job site to perform inspections, repairs, installations, or any other necessary service activities. Technicians should have easy access to all the relevant information, including job instructions, customer details, equipment manuals, and specific safety protocols.
During task execution, technicians may encounter unexpected challenges or complications that require quick thinking and problem-solving skills. For example, a technician installing a new electrical system in a residential building may discover outdated wiring that needs to be replaced. In such cases, the technician must assess the situation, communicate with the customer, and make the necessary adjustments for a successful installation.
Reporting and documentation
Once the tasks have been completed, it is crucial to document the work performed. This includes capturing the time spent on the job, materials used, any issues encountered, and the resolution provided. Accurate and detailed documentation forms the basis for invoicing, tracking service history, generating reports, and maintaining compliance records. It also serves as a valuable source of information for future reference and analysis.
For example, in a maintenance work order for a manufacturing plant, the reporting and documentation process would involve recording the date and time of the maintenance activity, the specific equipment serviced, the parts replaced, and any observations made by the technician. This information can then be used to track the equipment’s maintenance history, identify recurring issues, and plan for future maintenance needs.
Furthermore, detailed documentation is essential for regulatory compliance purposes. In industries such as healthcare or food service, work order documentation may need to adhere to specific standards and regulations to support the safety and well-being of customers and employees.
Steps in the work order process
The work order process is comprised of several steps, detailed as follows:
Request initiation
The work order process begins when a customer initiates a service request. This can be done through various channels, such as phone calls, emails, online portals, or mobile applications. It is important to capture all the necessary information during this stage for a smooth workflow.
During the request initiation phase, customer service representatives play a crucial role in gathering accurate and detailed information. They patiently listen to the customer’s needs, asking relevant questions to fully understand the scope of the job. This attention to detail helps in avoiding any misunderstandings or miscommunications later on.
Work order creation
Once the service request is received, a work order is created. This involves entering all the relevant details into the system, such as job description, customer information, location, and supporting documents. The work order is a central record that tracks the job’s progress from start to finish.
Creating a work order requires meticulous attention to detail. The person responsible for this task carefully reviews the information the customer service representative provided and cross-checks it with any additional documentation. This double-checking process ensures that all the necessary information is accurately recorded, minimizing the chances of errors or omissions.
Assignment and scheduling
After the work order is created, it is assigned to the appropriate technician or team based on availability, workload, and skillset. The scheduling process involves determining the optimal sequence of tasks and managing the workload to ensure timely completion without overburdening the resources. Clear schedule communication with the technicians is essential to avoid confusion and delays.
Assigning work orders requires a delicate balance of resource allocation. The person in charge carefully considers each technician’s workload, expertise, and availability. They also consider any urgent or high-priority jobs that may require immediate attention. This strategic planning ensures the workload is distributed evenly and efficiently among the team members.
Execution and completion
The technicians execute the tasks with the assigned work order and schedule. They follow the job instructions, use the necessary tools and equipment, and adhere to safety protocols. Regular communication with the back office, including updates on progress and any issues encountered, helps ensure smooth execution. Once the work is completed, the technician confirms it in the system.
During the execution phase, the technicians’ expertise and attention to detail come into play. They meticulously follow the job instructions, paying close attention to every detail to complete the work to the highest standards. In case of unexpected challenges or complications, the technicians promptly communicate with the back office, seeking guidance or support to overcome the obstacles.
Review and closeout
A review and closeout phase is necessary to finalize the work order process. This includes reviewing the work performed, ensuring quality standards are met, obtaining customer feedback, and, if required, obtaining signoff. Reviewing the process identifies areas for improvement and provides valuable insights for training and process refinement.
The review and closeout phase is a critical step in ensuring customer satisfaction. The person responsible for this phase carefully inspects the completed work, comparing it against the initial requirements and quality standards. They also contact the customer to gather feedback, addressing any concerns or issues that may have arisen during the process. This feedback is invaluable in continuously improving the quality of service provided.
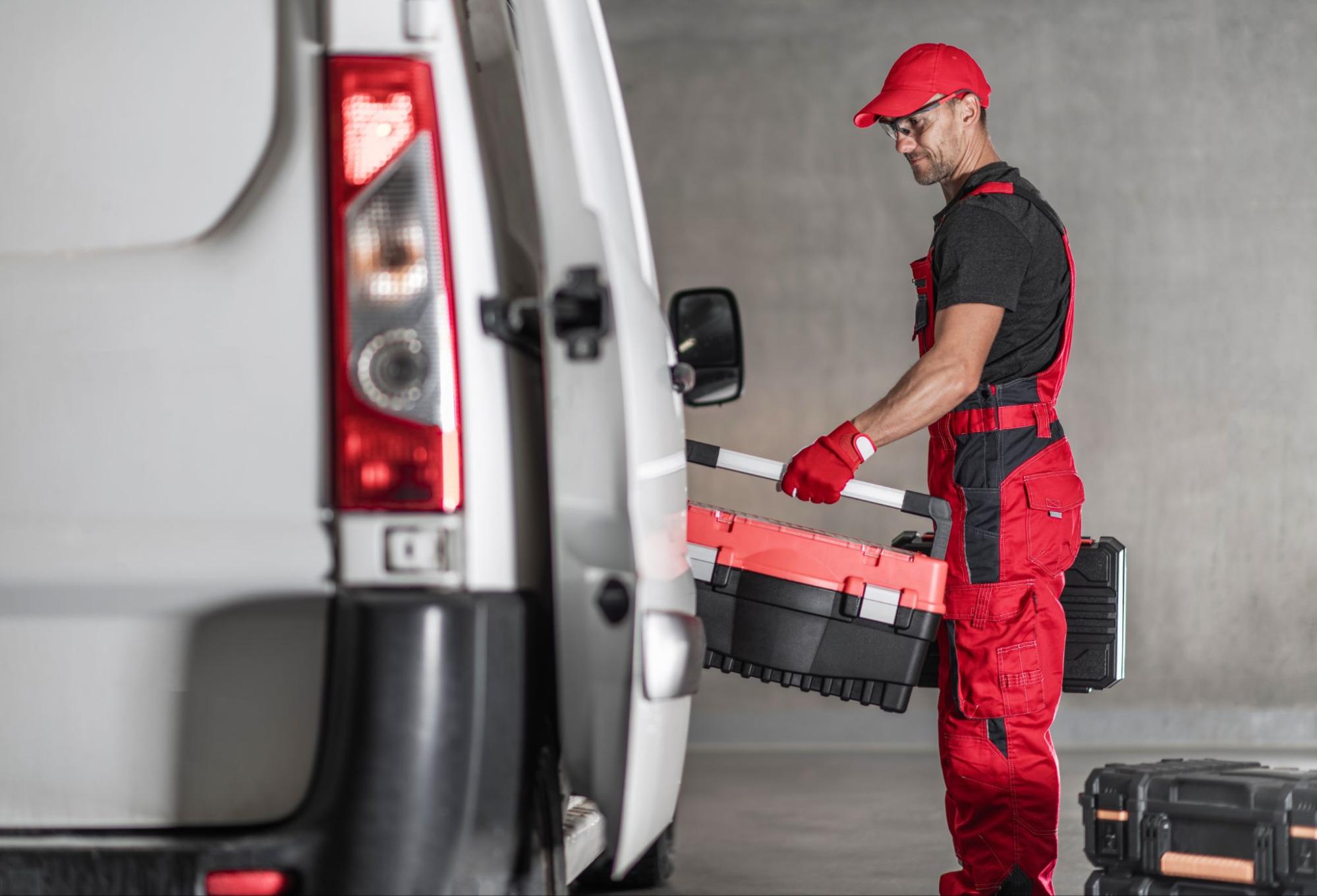
Implementing an effective work order process
There are several ways to implement an effective work order process, including:
Using field service management software
One key factor in implementing an effective work order process is leveraging field service management software. This technology provides a centralized platform for managing work orders, scheduling, dispatching, and tracking service activities. It streamlines communication, provides real-time visibility into field operations, and enables efficient collaboration between different stakeholders.
Field service management software offers many features and functionalities that enhance the work order process. For example, it allows technicians to access work orders on their mobile devices, eliminating the need for paper-based documentation and reducing the chances of errors. The software also automatically assigns work orders based on technician availability, skills, and proximity to the job site, ensuring efficient resource allocation.
Training field service personnel
Another critical aspect of implementing a successful work order process is training the field service personnel. They should be familiar with the standardized procedures, software tools, and best practices for customer service. Ongoing training and development programs keep technicians updated with the latest industry trends, improve their technical skills, and equip them to handle any challenges that may arise.
Training programs can cover many topics, including safety protocols, equipment handling, and customer interaction. By investing in comprehensive training, organizations can empower their technicians to deliver exceptional service, build strong customer relationships, and professionally represent the company. This not only improves customer satisfaction but also enhances the organization’s overall reputation in the field service industry.
Regular process evaluation and improvement
An effective work order process is not static but dynamic. Regular evaluation and improvement of the process are necessary to identify bottlenecks, eliminate inefficiencies, and enhance overall performance. This can be achieved through feedback from technicians and customers, analysis of key performance indicators, and benchmarking against industry best practices.
Organizations can establish a feedback loop with their technicians to gather valuable insights about the work order process. Technicians on the ground often have firsthand experience of the challenges and opportunities within the process. Organizations can make informed decisions to optimize the process and improve efficiency by actively seeking their input and incorporating their suggestions.
Additionally, organizations can leverage data analytics to analyze key performance indicators such as response time, resolution time, and customer satisfaction. This data-driven approach enables organizations to identify areas of improvement, set realistic goals, and measure the impact of process changes. Benchmarking against industry best practices also provides valuable insights and helps organizations stay ahead of the competition.
By continuously evaluating and improving the work order process, organizations can deliver the highest quality service to their customers. This commitment to excellence enhances customer satisfaction and drives company growth and success in the field service industry.
Conclusion
A well-implemented work order process is vital for field service organizations to deliver quality services promptly and efficiently. Organizations can optimize their operations, improve customer satisfaction, and achieve sustained success in the field service industry by understanding the basics, focusing on key components, following the defined steps, and using appropriate technology and training.
Do you need to boost your field service team? Schedule an introductory call with Field Nation today and discover why we’re the most convenient solution for connecting with thousands of skilled IT field service technicians.