In field service, optimizing work orders is crucial for maximizing efficiency and productivity. By streamlining processes and improving communication, businesses can ensure that work orders are executed effectively. In this article, we will explore the importance of work order optimization, the key elements of an optimized work order, strategies for optimization, and how to overcome challenges in the process.
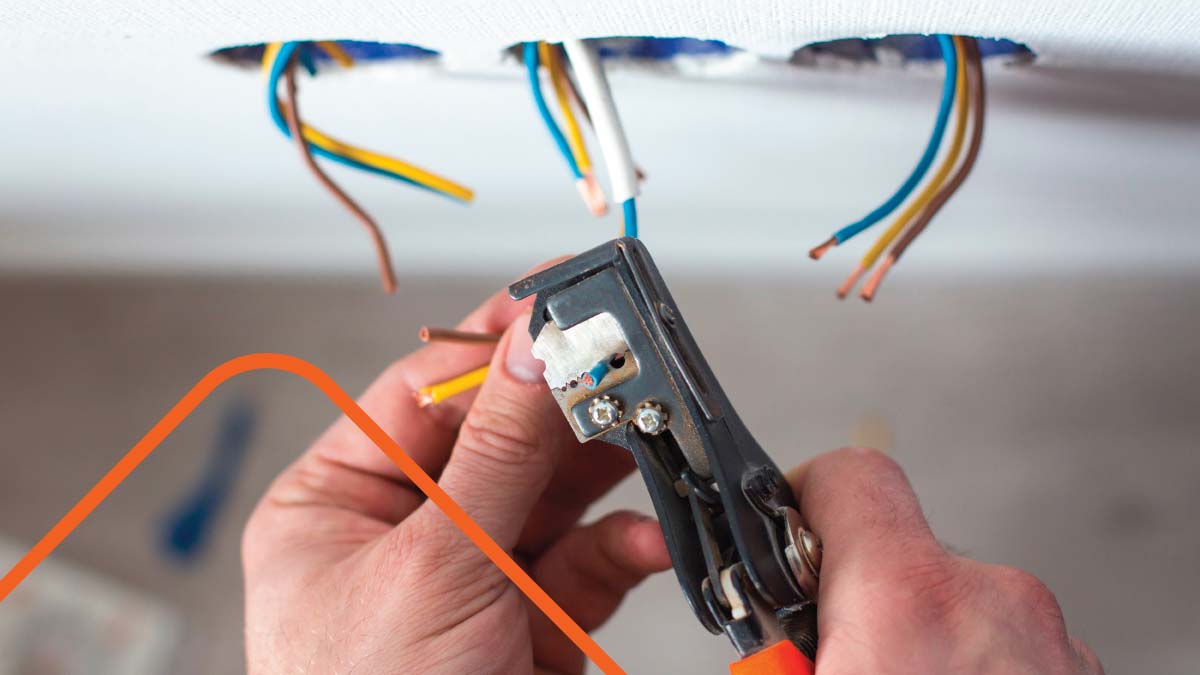
Understanding the importance of work order optimization
Work orders play a pivotal role in field service operations. They serve as a blueprint for technicians, outlining the tasks, materials required, and any additional instructions. Businesses can ensure that tasks are completed accurately and efficiently by optimizing work orders.
Work orders are not just a list of tasks but a roadmap guiding technicians through their day. Each one is carefully crafted to provide all the necessary details for successful project completion, from the specific tools needed to the exact steps to follow. Work orders are designed to streamline workflow and minimize errors.
Benefits of optimized work orders
Optimizing work orders offers numerous benefits to field service organizations. Firstly, it enhances productivity by eliminating unnecessary steps and ensuring technicians have all the information they need upfront. This reduces downtime and allows them to complete more jobs in a day.
Secondly, optimized work orders improve customer satisfaction. Businesses can provide more accurate service windows and minimize delays by accurately estimating the time required for each task and properly allocating resources.
Efficient work orders also contribute to a safer work environment. By clearly outlining safety procedures and equipment requirements, work orders help reduce the risk of accidents and prepare technicians for situations they may encounter.
Lastly, efficient work orders contribute to better cost control. With accurate time estimations and proper resource allocation, businesses can avoid unnecessary overtime and minimize expenses.
Key elements of an optimized work order
An optimized work order includes clear instructions and relevant details for seamless task execution. It promotes efficient workflow and minimizes errors for successful project completion. Important elements of optimized work orders are:
Detailed project descriptions
An optimized work order should include a detailed job description. This description should outline the specific tasks to complete and any special instructions or safety guidelines. Providing technicians with clear instructions minimizes confusion, enhances efficiency, and ensures tasks are completed correctly.
Accurate time estimations
Time is a valuable resource in field service, and accurate time estimations are crucial for work order optimization. Businesses can effectively plan their schedules and avoid unnecessary delays by providing technicians with realistic timeframes for each task. Factors such as travel time, task complexity, and any potential hurdles that may arise should be considered.
Proper resource allocation
Allocating the right resources to each work order is essential for efficient execution. This includes assigning the most qualified technicians to specific tasks, ensuring they have the necessary tools and equipment, and providing access to relevant documentation or manuals. Proper resource allocation minimizes rework, reduces errors, and enhances overall productivity.
Effective communication channels
Another key element of an optimized work order is establishing effective communication channels between technicians, supervisors, and customers. Clear lines of communication help resolve any issues that may arise during the execution of the work order. Whether through phone calls, emails, or a dedicated messaging platform, seamless communication ensures that everyone is on the same page and can promptly address any concerns.
Continuous monitoring and feedback
Continuous monitoring and feedback mechanisms play a vital role in work order optimization. By tracking the progress of tasks in real-time, supervisors can identify bottlenecks or delays and take corrective actions promptly. Additionally, collecting feedback from technicians and customers post-completion helps refine processes, improve service quality, and enhance overall customer satisfaction.
Strategies for work order optimization
Strategies for work order optimization are critical for enhancing productivity and streamlining operations. They help maximize efficiency, minimize downtime, and support timely completion of tasks. Work order optimization strategies include:
Implementing a prioritization system
A prioritization system helps businesses manage work orders based on their urgency and importance. Organizations can allocate resources accordingly by categorizing work orders as high, medium, or low priority and ensuring that critical tasks are addressed promptly. This avoids delays and prioritizes important customer needs.
Using field service management software
Field service management software offers advanced capabilities for work order optimization. These tools streamline communication, automate workflows, and provide real-time visibility into job progress. Organizations can use field service management software to improve collaboration, track job statuses, and efficiently manage work order schedules.
Streamlining communication channels
Effective communication is vital for work order optimization. Establishing streamlined communication channels between field technicians, the back office, and customers ensures that everyone has access to accurate and up-to-date information. This minimizes miscommunication, enhances collaboration, and speeds up the resolution of any issues that may arise.
Internet of Things
In addition to field service management software, organizations can also benefit from integrating Internet of Things (IoT) devices into their work order optimization strategies. IoT devices can provide real-time data on equipment performance, enabling predictive maintenance and proactive issue resolution. By leveraging IoT technology, businesses can reduce downtime, extend the lifespan of assets, and enhance overall operational efficiency.
Furthermore, when implementing a prioritization system, it is essential to consider the urgency of the work orders and their impact on overall operations. Some tasks may seem urgent but have minimal impact on the business, while others, though less urgent, could significantly affect productivity or customer satisfaction.
By taking a holistic view of work order prioritization, organizations can allocate resources to maximize efficiency and business outcomes.
Overcoming challenges in work order optimization
Overcoming challenges in work order optimization is essential for maintaining operational efficiency and meeting deadlines. It enables businesses to minimize disruptions, improve resource allocation, and ultimately enhance customer satisfaction. Some ways to overcome work order optimization challenges include:
Dealing with unpredictable field conditions
Field service teams often encounter unpredictable conditions that can impede work order optimization. These may include inclement weather, equipment failures, or unexpected delays. To overcome these challenges, businesses must have contingency plans, allowing for quick adaptation and alternative solutions when unforeseen circumstances arise.
One way to address unpredictable field conditions is by leveraging advanced technology such as IoT sensors. These sensors provide real-time data on environmental factors like temperature, humidity, and equipment performance. By analyzing this data, businesses can proactively identify potential issues and adjust work orders accordingly, minimizing disruptions and optimizing efficiency.

Managing a high volume of work orders
Managing a large volume of work orders can be challenging in industries with high demand. Organizations should implement efficient work order management systems to optimize this process, including automated workflows and load-balancing techniques. By effectively managing the influx of work orders, businesses can prevent backlogs and ensure timely job completion.
Another strategy for handling a high volume of work orders is to use predictive analytics. By analyzing historical data and patterns, organizations can forecast demand, allocate resources more effectively, and prioritize critical tasks. This proactive approach streamlines work order optimization and enhances overall operational efficiency.
Handling changes in real-time
Real-time changes can disrupt work order optimization. For example, a customer may request a change or additional task while a technician is on-site. To handle such situations, businesses should empower their technicians with decision-making capabilities, clear escalation processes, and the tools to adjust work orders on the fly. This ensures that customer requests are addressed promptly and efficiently
Additionally, a centralized communication platform can facilitate seamless coordination between customers, technicians, and back-office staff. This platform can enable instant updates, real-time notifications, and collaborative problem-solving, ensuring that any changes to work orders are communicated swiftly and accurately. By fostering transparent communication channels, businesses can enhance agility and responsiveness in real-time changes, ultimately improving customer satisfaction.
Conclusion
Optimizing work orders is vital for field service organizations seeking to maximize efficiency, productivity, and customer satisfaction. Businesses can improve their processes and deliver exceptional service by understanding the importance of work order optimization, implementing key elements in work order design, utilizing effective strategies, and overcoming challenges.
Ready to elevate your field service operations? Schedule an introductory call with Field Nation. Start your journey to maximizing efficiency, productivity, and customer satisfaction today.