Work Order Management (WOM) is an essential process that allows organizations to streamline operations and ensure timely task completion. Companies can enhance productivity, improve customer satisfaction, and reduce costs by effectively managing work orders. In this article, we will discuss the key aspects of WOM and explore best practices that can be implemented to maximize efficiency.
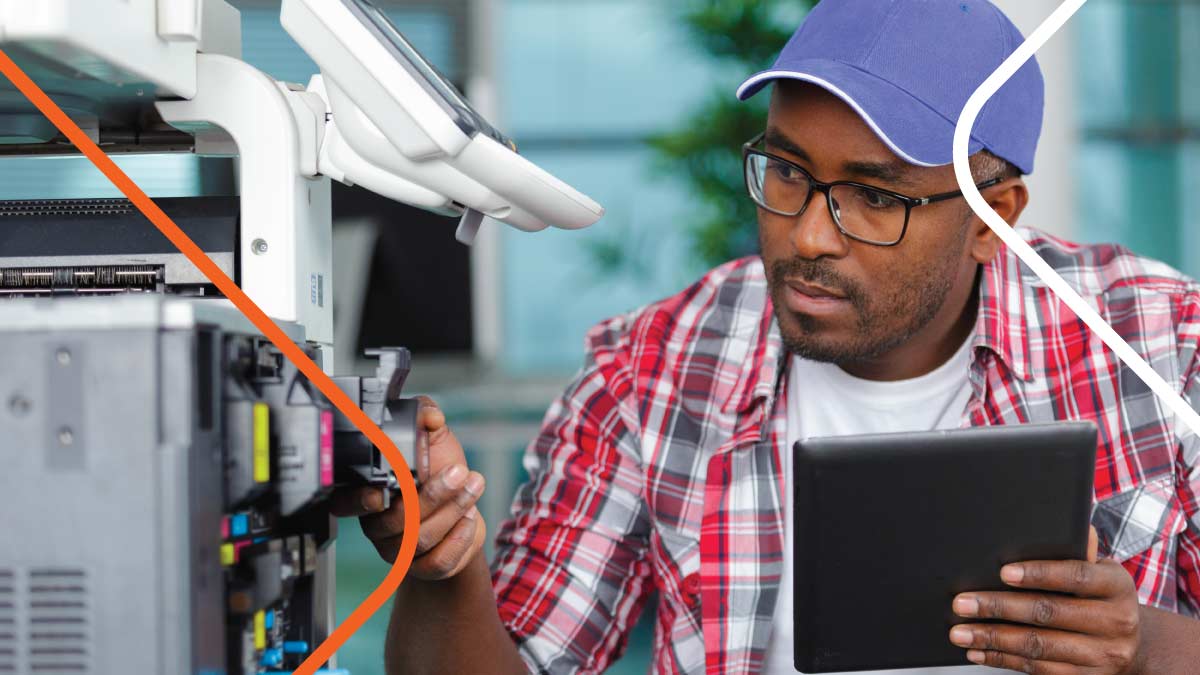

Understanding work order management
WOM is the systematic control and tracking of organizational tasks, assignments, and requests. It involves creating, assigning, and completing work orders to ensure smooth operations and service delivery. This process plays a crucial role in maintenance, construction, and customer support, where multiple tasks must be prioritized and executed.
Definition and importance of work order management
WOM is the process of planning, scheduling, and tracking work orders to promote efficient resource allocation and timely task completion. It provides organizations with a framework for managing their operations effectively, ensuring that work requests are addressed promptly and efficiently. By implementing a robust WOM system, companies can minimize downtime, improve accountability, and enhance productivity.
Key components of work order management
Successful WOM relies on various essential components. These include:
- Work order creation: The process of generating work orders to record and track specific tasks or assignments.
- Task assignment: Assigning work orders to the appropriate individuals or teams responsible for their completion.
- Priority management: Establishing priorities for work orders based on urgency, client requirements, or criticality.
- Task tracking: Monitoring the progress of work orders to ensure timely completion and identify potential bottlenecks.
- Resource allocation: Assigning the necessary resources, such as manpower, equipment, and materials, to work orders.
- Communication and collaboration: Facilitating effective communication and collaboration among team members involved in WOM.
WOM systems often include additional features to enhance efficiency and streamline processes. These features may include:
- Automated notifications: Sending automated notifications to stakeholders when work orders are created, assigned, or completed, keeping everyone informed.
- Integration with asset management: Integrating WOM with asset management systems to track and manage the maintenance and repair of equipment and facilities.
- Reporting and analytics: Generating reports and analytics to gain insights into work order performance, resource utilization, and areas for improvement.
- Mobile accessibility: Providing mobile access to WOM systems, allowing field technicians to receive and update work orders in real time.
Efficient WOM is essential for organizations to meet operational goals and deliver high-quality services. By implementing a comprehensive WOM system, companies can streamline their processes, improve communication, and ensure that tasks are completed on time, increasing customer satisfaction and overall success.
Establishing effective work order processes
Implementing well-defined work order processes is essential for efficient management. Organizations can minimize confusion, improve coordination, and provide consistent service delivery by creating a structured workflow.
Steps to create a work order process
An effective work order process can be established by following these steps:
- Standardize work order templates: Develop standardized templates to capture essential details such as task description, priority level, required resources, and deadlines.
- Define approval workflow: Establish a clear approval hierarchy so that the appropriate personnel review and authorize work orders.
- Automate workflow: Leverage technology solutions to automate the workflow, enabling seamless assignment, tracking, and notification of work orders.
- Establish reporting mechanisms: Implement reporting mechanisms to track KPIs and generate actionable insights for process improvement.
- Monitor and review: Regularly monitor and review the work order process to identify areas of improvement and address any bottlenecks.
Streamlining the work order process
Streamlining the work order process is crucial for maximizing efficiency and productivity. Here are some strategies to consider:
- Eliminate redundancy: Identify and remove redundant steps or processes that add unnecessary complexity to the workflow.
- Encourage communication: Foster effective communication channels to facilitate seamless collaboration and information sharing among teams.
- Implement real-time tracking: Use technology to enable real-time tracking of work orders, allowing stakeholders to monitor progress and intervene if necessary.
- Empower employees: Provide employees with the necessary training and resources to confidently execute their tasks.
- Regular performance reviews: Conduct periodic performance reviews to assess the work order process’s effectiveness and identify improvement opportunities.
Furthermore, it is important to consider the role of preventive maintenance in the work order process. By implementing a proactive approach, organizations can minimize the occurrence of unexpected equipment failures and breakdowns. This can be achieved by conducting regular inspections, performing routine maintenance tasks, and addressing any identified issues promptly.
Another aspect to consider is integrating a mobile application into the work order process. By leveraging mobile technology, organizations can empower their field technicians to access work orders, update task statuses, and communicate with the central system in real time. This improves efficiency, enables faster response times, and enhances customer satisfaction.
Best practices in work order management
Implementing best practices can significantly enhance the effectiveness of WOM. Here are some key areas to focus on:
Prioritizing work orders
Every organization must prioritize work orders based on their urgency and importance. By establishing a clear prioritization framework, companies can give critical tasks immediate attention, minimize delays, and optimize resource allocation. Prioritization can be based on customer impact, safety considerations, and contractual obligations.
For instance, in industries where safety is paramount, work orders for safety inspections or equipment maintenance may be given the highest priority. This ensures that potential hazards are promptly addressed, reducing the risk of accidents and promoting compliance with safety regulations.
Leveraging technology in work order management
Technology plays a crucial role in modern WOM. Organizations can streamline administrative tasks, improve data accuracy, and enhance communication by adopting a digital WOM system. Using mobile access, automated notifications, and real-time tracking can significantly improve efficiency and reduce manual errors.
Moreover, advanced technologies like the Internet of Things (IoT) can revolutionize WOM. IoT devices embedded in equipment can automatically generate work orders when maintenance is required, eliminating manual intervention. This saves time and promotes proactive maintenance, preventing costly breakdowns and minimizing downtime.
Training and skill development for work order management
Employee training and skill development are essential for effective WOM. Training programs should focus on familiarizing employees with work order processes, system usage, and relevant industry practices. By enhancing employees’ competencies, organizations can ensure that work orders are handled professionally, improving quality and customer satisfaction.
Furthermore, cross-training employees in different aspects of WOM can provide flexibility and agility in handling various work orders. This allows organizations to efficiently allocate resources and respond to changing demands, promoting smooth operations and customer satisfaction.
Challenges in work order management
Despite the benefits, organizations often encounter challenges when implementing WOM. Identifying and addressing these challenges is crucial to maximize its effectiveness.
One significant challenge in WOM is integrating different organizational departments and systems. Work orders often require input and action from multiple teams, such as maintenance, operations, and finance. Coordinating these efforts can be complex, especially when each department has its own set of priorities and processes.
Another common obstacle is the lack of real-time visibility into work order status and progress. Without a centralized system that provides up-to-date information on each work order’s status, delays and miscommunications can occur, leading to inefficiencies and potential errors.
Common obstacles in implementing work order management
Some common obstacles include:
- Lack of standardization: Inconsistent work order formats and processes can lead to confusion and miscommunication.
- Resistance to change: WOM systems may face resistance from employees unfamiliar with new technologies or unwilling to adapt to new processes.
- Poor communication: Inadequate communication channels can hinder coordination and collaboration among team members.
Solutions to overcome work order management challenges
To overcome these challenges, organizations can:
- Standardize work order templates: Develop standardized templates that capture essential information consistently across all work orders.
- Provide comprehensive training: Offer training programs to familiarize employees with new WOM processes and systems.
- Enhance communication channels: Implement robust communication platforms that facilitate seamless information sharing and collaboration.
Measuring success in work order management
Measuring key performance indicators (KPIs) is vital to assessing WOM’s effectiveness and identifying areas for improvement. Organizations can gain valuable insights into their operational efficiency and service quality by tracking and analyzing these metrics.
Effective WOM is essential for maintaining smooth operations and supporting timely task completion. It involves a systematic approach to handling work orders, from creation to closure, while prioritizing urgent requests and optimizing resource allocation.

Key performance indicators for work order management
Some relevant KPIs include:
- Work order completion rate: The percentage of work orders successfully completed within the designated timeframe.
- Response time: The time taken to acknowledge and initiate work on a newly created work order.
- Mean time to repair (MTTR): The average time taken to restore operations after a work order is initiated.
- Customer satisfaction: Measuring customer feedback and satisfaction levels to assess service quality.
These KPIs provide a comprehensive view of the efficiency and effectiveness of WOM processes. They allow organizations to identify bottlenecks, streamline workflows, and enhance performance.
Continuous improvement in work order management
WOM should be viewed as an ongoing process of continuous improvement. Regularly review existing workflows, gather feedback from stakeholders, and incorporate suggestions for refinement. Continuously adapting and optimizing WOM processes can improve efficiency, reduce costs, and enhance customer satisfaction.
Furthermore, embracing technology solutions such as WOM software can streamline operations, automate repetitive tasks, and provide real-time visibility into work order status. Leveraging data analytics and predictive maintenance capabilities can help organizations proactively address issues, minimize downtime, and improve asset reliability.
Conclusion
Effective WOM is essential for organizations to optimize operations and deliver exceptional service. Companies can streamline their operations, enhance productivity, and exceed customer expectations by understanding the key components of WOM, establishing effective processes, implementing best practices, and continuously measuring performance.
Embracing technology and focusing on communication, collaboration, and skill development are vital aspects of successful WOM. Organizations can significantly improve their WOM processes by proactively embracing best practices and addressing challenges.
Need help in supporting your work orders? Schedule an introductory call with Field Nation today and discover why we’re the most convenient solution for connecting with thousands of skilled IT field service technicians.