Work order management is crucial in ensuring the smooth execution of tasks and projects in various industries. Organizations can improve productivity, reduce costs, and enhance customer satisfaction by effectively managing work orders. This article will explore the definition, importance, key components, best practices, challenges, and the future of work order management.

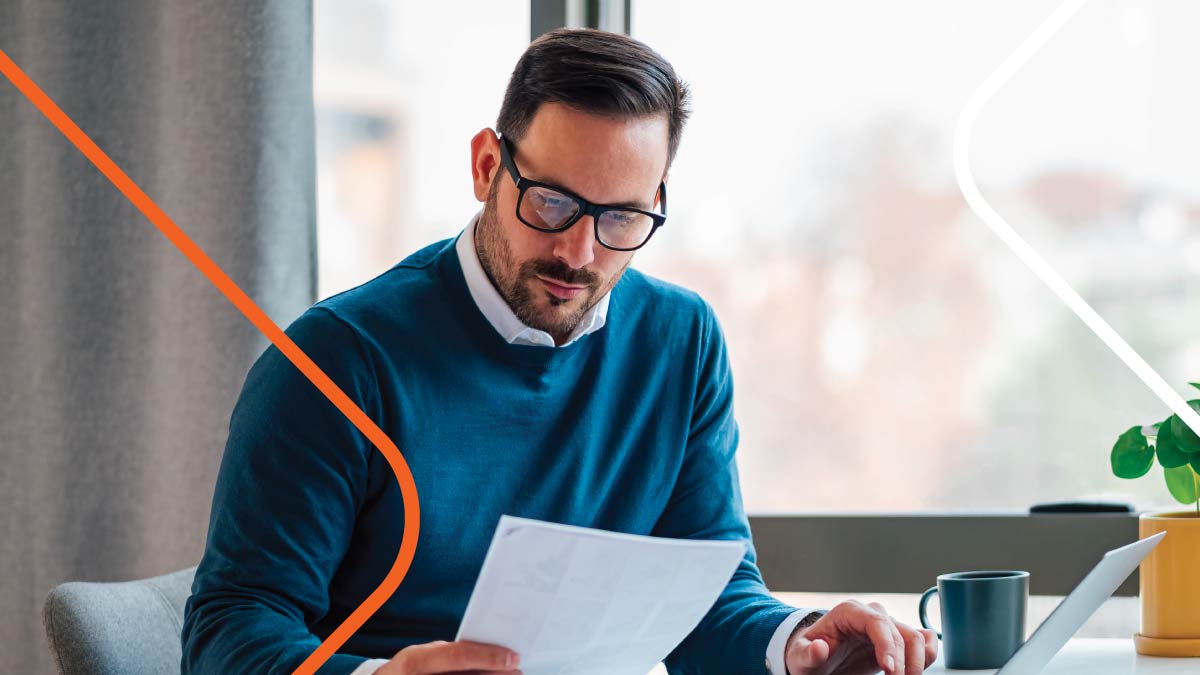
Understanding work order management
It is important to define the concept of work order management to fully understand its importance in various industries.
Work order management is not just a simple administrative task, but a critical process that can make or break an organization’s success. It involves much more than creating and tracking work orders.
Definition and importance of work order management
Work order management is the backbone of efficient operations. It creates, organizes, prioritizes, and tracks work orders within an organization. Work order management involves efficiently allocating resources, assigning tasks, and monitoring work progress to ensure timely completion.
Effective work order management is essential as it helps optimize operations and ensures that tasks are executed smoothly. Organizations can minimize downtime, improve efficiency, and provide excellent customer service by creating a systematic approach to managing work orders.
Imagine a scenario where work orders are not properly managed. Chaos would ensue, with tasks being forgotten or delayed, resources being misallocated, and customer satisfaction plummeting. Work order management ensures that every task is accounted for, every resource is utilized effectively, and every deadline is met.
Key components of work order management
Work order management comprises several key components of successful implementation and execution. Let’s take a closer look at these components:
- Work order creation: Work orders are the starting point of any task, project, or service request. They include important details such as the task description, priority level, deadline, and additional requirements. A well-crafted work order sets the foundation for a successful project.
- Resource allocation: Efficient resource allocation is vital to assign the right people with the necessary skills and equipment to each work order. This component requires careful consideration of the availability and capabilities of resources to maximize productivity.
- Task assignment: Once a work order is created, tasks must be assigned to individuals or teams responsible for completion. Clear communication and proper delegation are essential to avoid confusion or duplication of efforts.
- Progress tracking: Regular monitoring of work orders allows organizations to stay updated on the status of tasks, identify delays or bottlenecks, and take necessary actions to keep projects on track. This component ensures that projects progress smoothly and issues are addressed promptly.
- Documentation: Proper documentation of work orders is not just a bureaucratic formality but a crucial aspect of work order management. It helps maintain a comprehensive record of tasks, facilitate future reference, and drive accountability. Documentation also aids in analyzing past projects and identifying areas for improvement.
Each component plays a vital role in the overall success of work order management. By paying attention to detail and implementing efficient processes, organizations can streamline operations and achieve higher productivity and customer satisfaction.
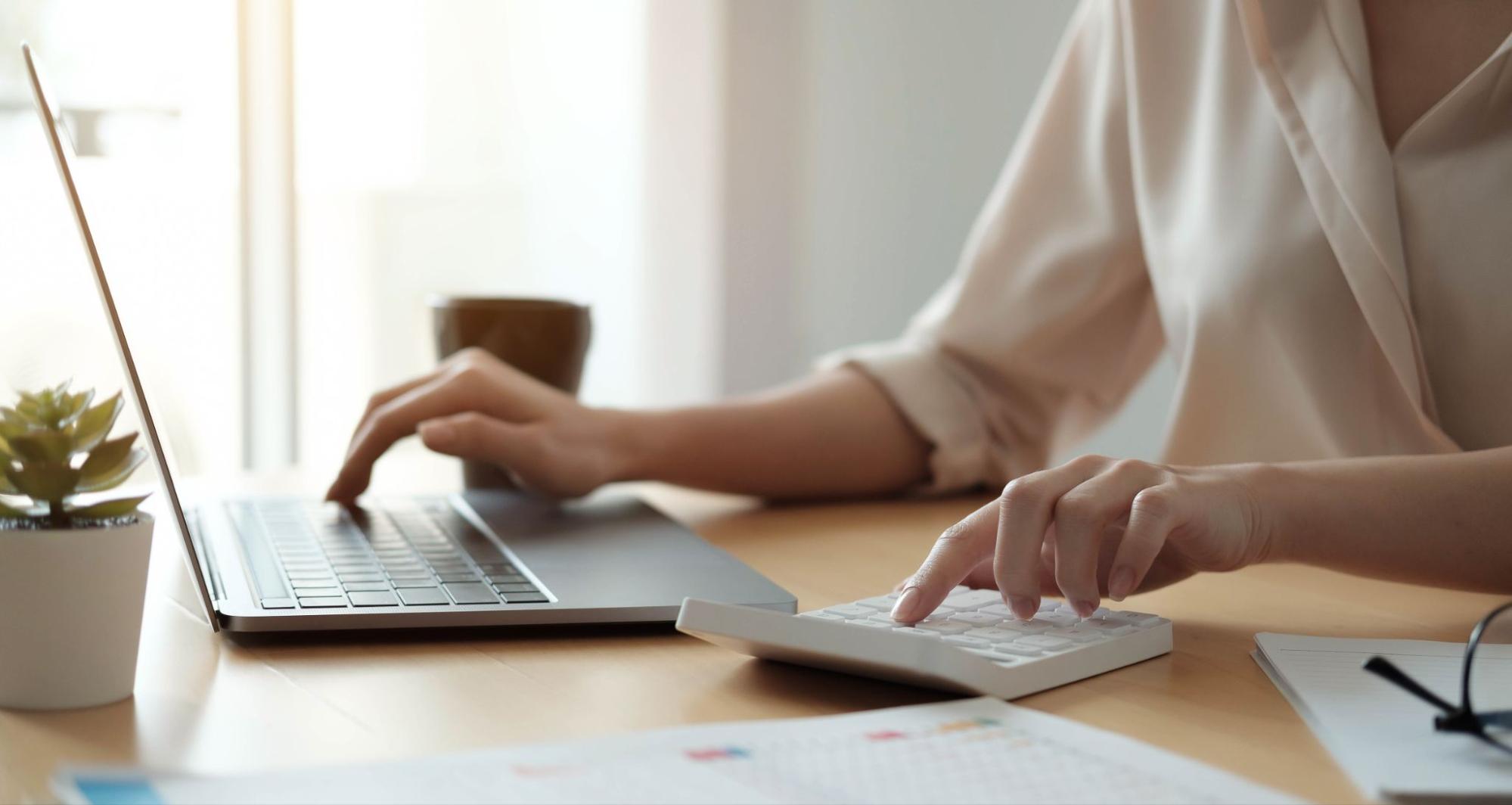
Best practices for efficient work order management
Efficient work order management is crucial for organizations to maintain operational effectiveness and meet customer demands. By implementing streamlined processes and leveraging technology, companies can ensure the timely completion of tasks and optimal resource utilization.
Implementing best practices in work order management can significantly improve efficiency and productivity. Here are a few strategies organizations can adopt:
Streamlining work order processes
To streamline work order processes, organizations can:
- Standardize work order templates for consistency and clarity.
- Establish clear communication channels to facilitate effective collaboration.
- Automate routine tasks through the use of workflow management systems.
- Implement a centralized database for easy access to work order information.
Standardizing work order templates improves communication, helps track progress, and identifies bottlenecks in the process. Clear communication channels keep all stakeholders on the same page, reducing the chances of errors and delays in task execution.
Leveraging technology in work order management
The integration of technology can greatly enhance work order management practices. Organizations can leverage technology by:
- Using work order management software to automate processes and improve efficiency.
- Implementing mobile applications to enable real-time updates and communication.
- Integrating IoT devices to monitor equipment performance and trigger work orders for maintenance or repairs.
Work order management software offers features such as task assignment, progress tracking, and reporting, which streamline operations and provide valuable insights for decision-making. Mobile applications empower field technicians to access work orders, update statuses, and communicate with the team seamlessly, ensuring swift resolution of issues.
Challenges in work order management
While work order management brings numerous benefits, it also presents challenges. Recognizing and addressing these challenges is essential for successful implementation.
One key challenge in work order management is integrating various organizational departments and teams. Different teams may often have their own ways of handling work orders, leading to a lack of standardized processes and documentation. This can result in confusion, delays, and errors in work order execution. Organizations must streamline their processes and keep all teams aligned in their approach to work order management.
Common obstacles in implementing work order management
Some common obstacles organizations may encounter when implementing work order management include:
- Lack of standardized processes and documentation.
- Inadequate communication and coordination between teams.
- Resistance to change from employees.
- Insufficient training and knowledge about work order management systems.
Another challenge in work order management is employees’ resistance to change. Implementing a new system or process can be met with skepticism and pushback from staff members comfortable with the existing way of doing things. Organizations must address this resistance through effective change management strategies, clear communication, and employee involvement in the transition process.
Strategies to overcome work order management challenges
Organizations can overcome work order management challenges by adopting the following strategies:
- Create and communicate clear work order policies and procedures.
- Provide comprehensive training and support to employees during the transition.
- Regularly review and update work order management processes to address any inefficiencies.
- Encourage employee engagement and involvement in the improvement of work order management practices.
Furthermore, organizations can leverage technology solutions such as work order management software to streamline processes, improve communication, and enhance visibility into work order status and progress. By investing in the right tools and resources, organizations can overcome the challenges associated with work order management and drive efficiency and productivity.
The future of work order management
As technology continues to advance, the future of work order management holds great potential for improvement and innovation.
Work order management systems are poised to undergo significant transformations. Integrating cutting-edge tools and methodologies promises to revolutionize how companies handle their maintenance operations, leading to increased efficiency and cost savings.
Emerging trends in work order management
Some emerging trends in work order management include:
- Increased use of predictive analytics to optimize maintenance schedules and prevent equipment failures.
- Integrating artificial intelligence (AI) for intelligent work order routing and task prioritization.
- Implementation of augmented reality (AR) for remote assistance and troubleshooting.
Moreover, adopting Internet of Things (IoT) devices in work order management is gaining traction. These devices allow real-time equipment performance monitoring and seamless communication between systems. This interconnected approach enables companies to proactively address issues before they escalate, leading to smoother operations and enhanced customer satisfaction.
The role of AI and automation in work order management
AI and automation are set to revolutionize work order management by:
- Automating repetitive tasks to free up resources to focus on more complex activities.
- Enhancing predictive maintenance capabilities, reducing downtime, and increasing equipment lifespan.
- Enabling proactive decision-making through data analysis and insights.
Furthermore, implementing machine learning algorithms in work order management systems allows continuous improvement and adaptation to changing circumstances. Analyzing historical data and patterns allows AI-powered solutions to optimize workflows, leading to more efficient resource allocation and streamlined processes.
Conclusion
Work order management is essential for smooth operations and success across various industries. By defining its importance, understanding its key components, and implementing best practices, companies can significantly enhance their productivity, reduce costs, and improve customer satisfaction.
Ready to take your company to the next level? Schedule an introductory call with Field Nation today and discover why we’re the most convenient solution for connecting with thousands of skilled IT field service technicians.